Page 1 of 2
Posted: Thu Jan 19, 2006 4:33 am
by morten
Hi Bo
Nice looking reg there. There is a few pics on my website of Chris Bayley milling a chanter for a key:
http://www.pipers.dk/
Look under "archive"
- He used a milling attachment for the lathe, and a homemade bit i think.
/Morten
Posted: Thu Jan 19, 2006 4:37 am
by billh
Hi Bo:
There's some discussion of keyway cutting in DMQuinn's Pipers' Review article on keywork and springs.
I think a slot cutter/end-mill is a more reliable tool. I'd make sure the mill cuts on the end as well as the sides. My own suggestions include a nice firm holding arrangement to minimize chatter and movement, and cutting the keyway with multiple shallow passes. That should reduce tearout, chipping, and other mischief.
regards
Bill
Posted: Thu Jan 19, 2006 5:49 am
by Tony
Did you align the grain before cutting the keyblocks?
Previous discussion:
http://chiffboard.mati.ca/viewtopic.php ... c12bc89da1
Finishing Light Woods
Posted: Thu Jan 19, 2006 6:55 am
by Mike Hulme
Hi Bo,
Linseed Oil is the best finish for bare wood that is going to get handled. I use it on violin necks. Rub it on sparingly with a wad of newspaper and really push it deep into the wood. Let it dry and harden for a couple of days, burnish it up with some more wadded newspaper, and then repeat the whole process until you get a nice sheen on the wood. If it doesn't get the sheen it will need longer to dry between coats.
Posted: Thu Jan 19, 2006 7:07 am
by billh
Linseed oil is nice, but it can darken light wood considerably.
If you want the mounts to stay "white", you might try a bleached shellac sealer, with a coat of carnauba-blend wax on the outside. The "woodturner's stick" wax sticks leave a nice shine on light woods without darkening them, and the shellac can help protect and seal in case the wax gets worn.
Bill
Posted: Thu Jan 19, 2006 7:59 am
by nwhitmer
Here is a trick I learned from Patrick Olwell, who himself learned it from Michael Copeland: use a metal lathe & mount the work between centers. Put a cutting tool of the correct width (I use a 1/8" wide t-section cutoff blade) horizontally in the tool rest. Line up the work so the intended slot is next to the cutting tool. Lock the spindle so it won't turn. Hand crank the carriage to move the cutter back & forth, and the compound rest to advance the tool further into the work after each backwards (noncutting) pass. I go in about .010" per cutting pass, .015" if I'm feeling feisty.
Makes a very clean accurate slot & so far I have had no trouble with tearouts. Also avoids the use of Rotataing Blades, which make me uneasy.
Nick
Posted: Thu Jan 19, 2006 8:25 am
by billh
Thanks Nick. I also cut slots between centres on the lathe, with the chuck locked, but I use a slot-cutting rotary tool (a flexible shaft tool mounted in the tool rest) instead of a T-shaped cutting tool. I still cut the slot by moving the tool rest along the lathe bed, advancing the cutting edge a few thousandths per pass. Your method has the advantage, I expect. of avoiding the chatter issue altogether.
Posted: Thu Jan 19, 2006 9:00 am
by Kevin Popejoy
My method has some similarities. I mount the chanter or reg between centers on my wood lathe, the blocks centered uppermost and the spindle locked. I have a fixture that I mount to the bedways that's basically a U shaped box with rails along the top edge. These rails are aligned parallel to the body of the regulator. The spacing of the rails accomodate the base of my high speed plunge router. With the appropriate bit and careful alignment I cut the keyways by sliding the router along the rails. I take a few passes with the cutter, adjusting the depth using the plunge feature on the router. This is also the setup I use for cutting the key seats, which is accomplished by mounting the fixture perpendicular to the chanter or reg and cutting a flat seat across the face of the body. If you're interested I can post of photo of the setup.
Kevin
Posted: Thu Jan 19, 2006 10:19 am
by John Mulhern
VERY nice work, bo!

I'm curious...how were you holding it on, and feeding it in the drill press? Palmgren type milling attachment??? If the fixture was sturdy, I'd suspect concentricity of the saw rather than its surface speed...especially if a drill chuck with substantial runout was used to mount it. Those things are notorious for chipping & breaking teeth.
Posted: Thu Jan 19, 2006 11:12 am
by uillmann
cutting keyways
Posted: Thu Jan 19, 2006 12:57 pm
by giggleswicksam
Phew! All that technology. We use a razor saw and an old screwdriver. . . .
Sometimes I just bite it out with my teeth . . .
Posted: Thu Jan 19, 2006 1:19 pm
by pudinka
hey Uillmann -
Is that real boxwood on the lathe or a "substitute" boxwood? 'tis very nice looking. Is there any kind of finish on it at that point or was anything done for that coloring (oil, nitric acid or heating - as i have read)? It will darken some with age - yes?
Re: cutting keyways
Posted: Thu Jan 19, 2006 2:31 pm
by Joseph E. Smith
giggleswicksam wrote:Phew! All that technology. We use a razor saw and an old screwdriver. . . .
Sometimes I just bite it out with my teeth . . .
Yes. But then you have the experience behind you to insure your better dental health.

Re: cutting keyways
Posted: Thu Jan 19, 2006 2:31 pm
by Joseph E. Smith
giggleswicksam wrote:Phew! All that technology. We use a razor saw and an old screwdriver. . . .
Sometimes I just bite it out with my teeth . . .
Yes. But then you have the experience behind you to insure your better dental health.

Posted: Thu Jan 19, 2006 2:41 pm
by Doogie
uillmann wrote: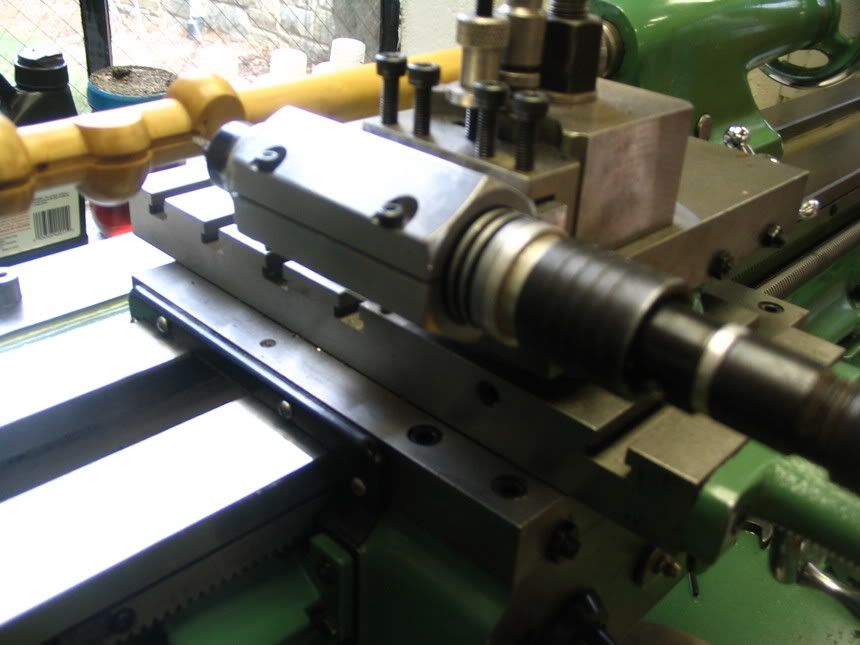
I like uillmann's set up, What kind of lathe is this...
I use a very large drill press with a cross sliding mill vice attached to it... I used to use the razor saw and screw driver/chisel method, that works as well...