This is great that so many folks are making their own whistles. I've been at it for a few years now. For those of you in the US using 1/2" CPVC schedule 80 hot water pipe (the off white stuff) that are having issues with Guido's suggested mouthpiece configuration, I have a few solutions you might want to try.braccio wrote:I am having some trouble flexing the 30 mm section of the windway cover enough for it to snap over the main pipe. Has anyone come up with a way to do this?
That pipe is designated CTS or copper tubing size for good, if not obvious, reasons. The outside diameter matches the size of traditional copper plumbing fittings. So you can use a copper coupler meant for joining pieces of 1/2" copper water pipe. It fits nicely right over the cpvc. There are two types of couplers. One has a dent in the middle clearly visible on the outside which serves to limit the insertion length of the two copper pipes it is designed to join. You can use those but may have to file the dent on the inside, your choice. The second type has no dent, works like a charm
The second suggestion is to use 1/2" schedule 40, 600 psi, pvc pipe as the outer mouthpiece. It has an inner diameter of 5/8", the same as the outer diameter of the cpvc. You may want to take a short piece of your cpvc with you to the hardware store to do a test fit. The internal diameters of this pipe can vary, the outside diameters are what is standardized.
My third suggestion is to go to a hobby shop which sells K&S brass tubing. The 21/32" size fits right over the cpvc too. If that size is not in stock, you probably have another whistle maker in the area.
A fourth suggestion is to use a cpvc pipe coupler. They have a ring inside which again limits the insertion distance for joining pipes. That can easily be drilled-out with the appropriate sized drill bit. I use forstner bits for this. Make sure you clamp the work piece so it doesn't spin as you drill. Cpvc heats up fast, stinks (probably kills brain cells too) and can cause some calamity if you aren't careful.
By the way, all of these can also be used as couplers for two piece whistles as well. Not the best choices for tuning slides though as the wall thickness of the pipe can leave a significant bore expansion at the point the tubes seperate causing tuning issues (think K&S brass on the inside). Some are more elegant than others.
Here is a photo of a few of my early whistles which use those materials.
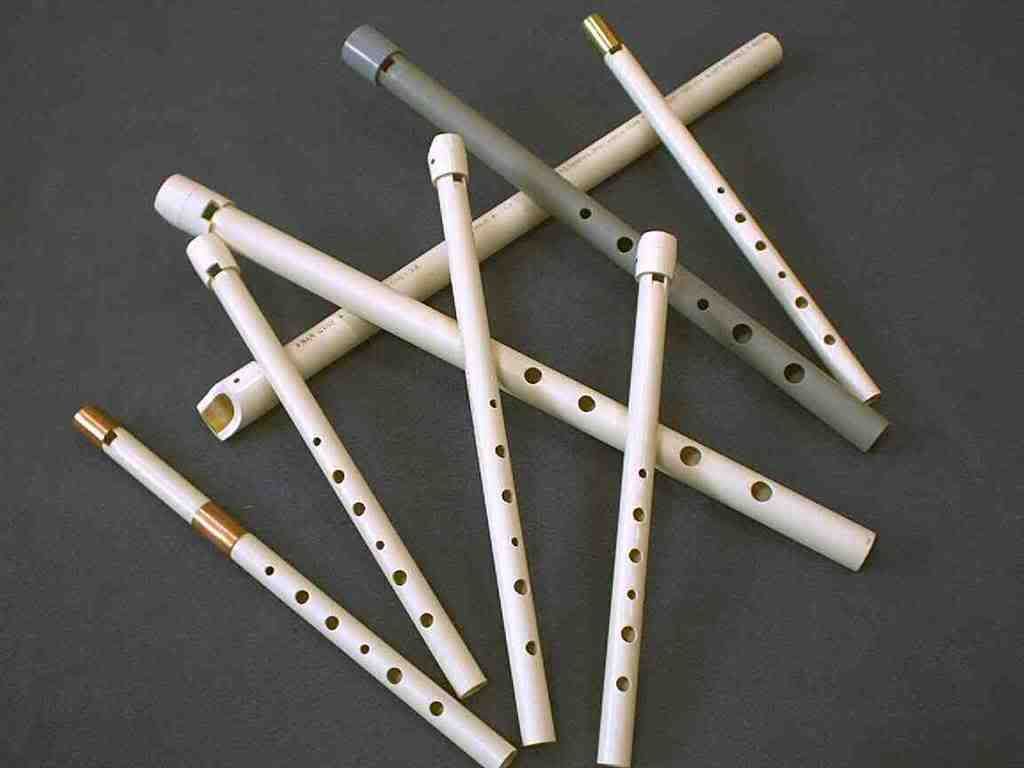
And remember that cpvc/pvc dust is not a good thing to inhale. Work safe and have fun.
Feadoggie